
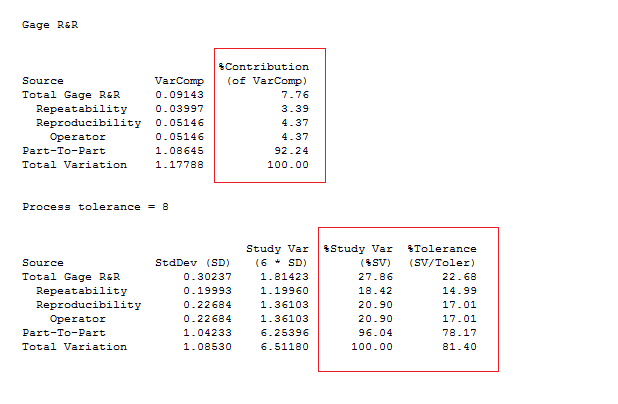
Pass Fail simply means there are only 2 results possible and are common when validating visual and functional tests.Ĭontinuous type studies are common in dimensional characteristics and functional tests that yield a test value. MSA studies are split into two main categories:
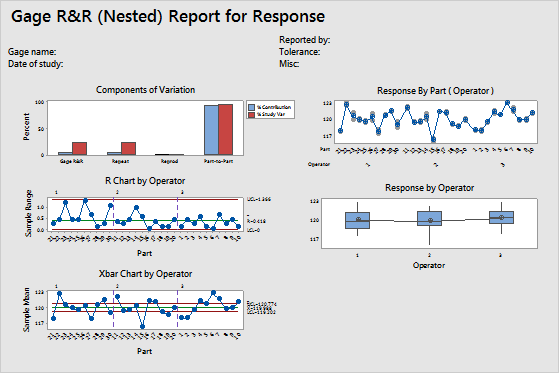
The act of confirming that your measurement equipment is adequate for your operation is called Measurement System Analysis (MSA).
#Type 1 gage study minitab how to
How to Execute a Gage R&R Study with Minitab? Part 2 The best way to demonstrate if the measurement system is the right one for your process is by running a Gage R&R study! So this story is all well and good right? But what does it mean for all engineers? Well if you have any issues were quality and production are not aligned then take a look at how you are currently measuring and if the issue is simply that the real process variation is being washed out by the operator and measurement equipment variations. Image taken from Optical Gaging Products To assure measurement consistency I programmed the company's automatic inspection system to use a routine and built fixtures to make sure that all samples were always placed in the same position when being measured. So if we can eliminate the VO variation by having everyone use the same method and if we eliminate the Equipment Variation by calibrating our equipment then the only variation that remains is the Real process variation. VO Operator Variation is eliminated with training, assuring everyone measures the same and when possible and ideally by using automatic systems which are independent from who measures. This means that our results are real and accurate.
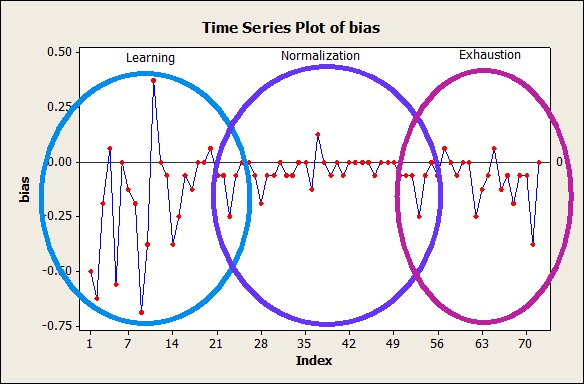
I bet you can imagine the frustration the technician felt every time he ran that machine. The problem was the machine technician was tasked with manually adjusting, taking samples, measuring them in an optical system and then once he was confident the part was fine he provided the finished process samples to quality who measured and then told the technician he was still off. Our Pad Printing process and quality commonly disagreed because according to quality inspectors the logo was misprinted and out of tolerance. These usually involve cosmetic defects such as smudges and misprints but occasionally they also involve very strict controls on the X and Y position of the logo. These Logos are usually not functional but since they are a client's brand they usually have very strict quality requirements. Ideally, both percentages should be 100 percent, but generally, the rule of thumb is anything above 90 percent is quite adequate.I had the opportunity to work in a Pad Printing Operation.įor engineers unfamiliar, a pad printing machine is an automatic printing equipment that usually stamps products with a logo. Reproducibility means that different operators, measuring the same thing, using the same gage, should get the same reading every time.Īttribute gage R&R reveals two important findings – percentage of repeatability and percentage of reproducibility. Repeatability means that the same operator, measuring the same thing, using the same gage, should get the same reading every time. The R&R stands for repeatability and reproducibility. The tool used for this kind of analysis is called attribute gage R&R. Hence, it is important to quantify how well such measurement systems are working. One example is quality control inspectors using a high-powered microscope to determine whether a pair of contact lens is defect free. However, such measurement systems are seen throughout industries. This is because it is very difficult for all testers to apply the same operational definition of what is “good” and what is “bad.” Most problematic measurement system issues come from measuring attribute data in terms that rely on human judgment such as good/bad, pass/fail, etc. There will always be some measurement variation that is due to the measurement system itself.
